ROHAN GODIYAL
LATEST PROJECTS






Project | 01
Project | 01 MODULAR ROBOT (MODBOT)
​
​Skills Acquired :Softwares( SOLIDWORKS, MATLAB), Programming( Arduino, Processing, MATLAB), Xbee Configuration and PCB printing.
​
The key idea here is to make a small module/unit which is controlled wirelessly by someone remotely or in a more advanced stage is itself intelligent enough to control its own individual locomotion using learning algorithms just based on given input functioning parameters. Further being equipped with linking capability it must be able to attach or detach itself from other identical/ non-identical modules (specialized modules) such that it forms a reconfigurable structure, mechanism or robot in order to complete an assigned task ranging from small scale such as learning/fun tasks for kids to advanced ones such as an unknown terrain exploration in outer space. Such a project or model falls in the category of modular robotics which is again itself a sub category of reconfigurable robotics. This product serves the demand of a recently emerging need for the bots with multitasking ability with considerably well efficiency rather than focusing on just one specific task per specialized bot.
​
STATUS: ONGOING
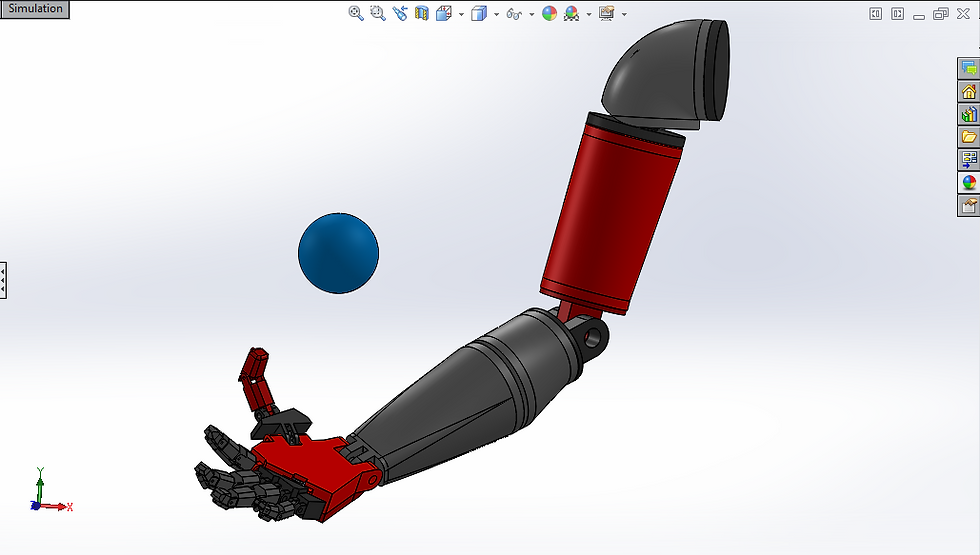




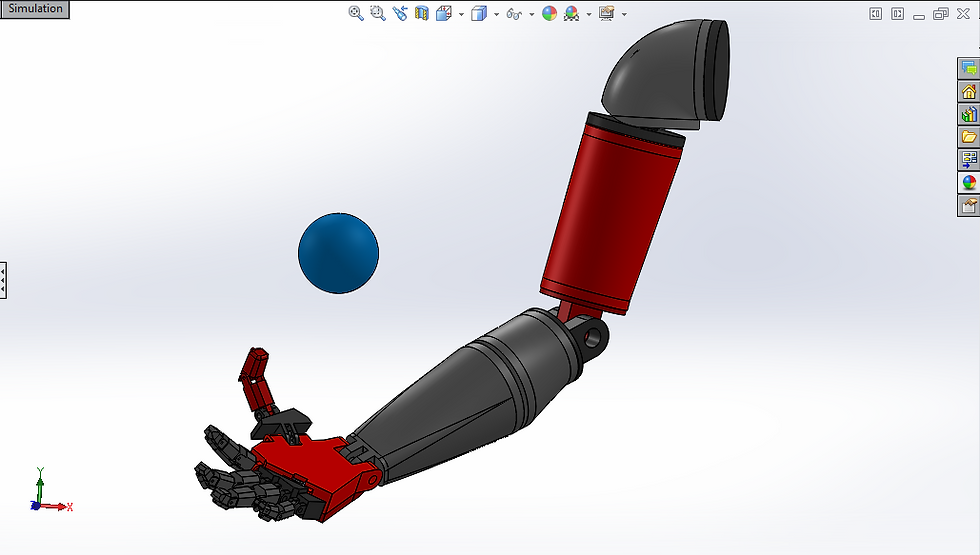




Project | 02
Project | 02 ARMBOT
​
The project began with an aim to design Arm structure for a Humanoid / Android bot that is to design a programmable arm that can be controlled in a variety of ways from an exoskeleton, gesture, or an interface on any computer device. With a wide scope of applications ranging from assisting armbot to a surgical arm the major area of interest is to understand the human arm structure in terms of design, dynamics and gripping action and incorporate it's evolutionary efficiencies into the Robotic Arm as much as possible. Though the major challenge would be to incorporate precision at every level possible We have made progress through the CAD modelling which i have been a contributor to extensively and the simulation of kinematics of the structure on GAZEBO simulation platform in ROS. The fabrication is under progress and the first prototype is expected to be complete soon.
​
STATUS: ONGOING


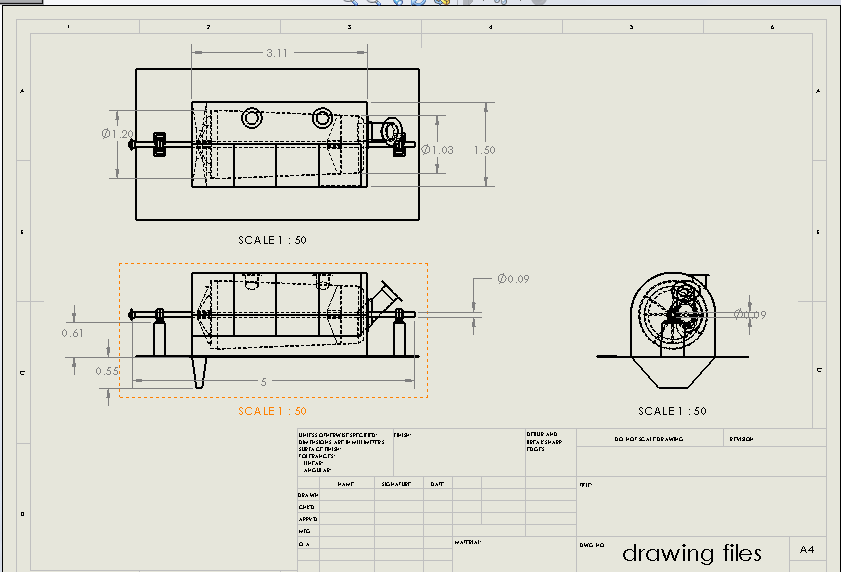

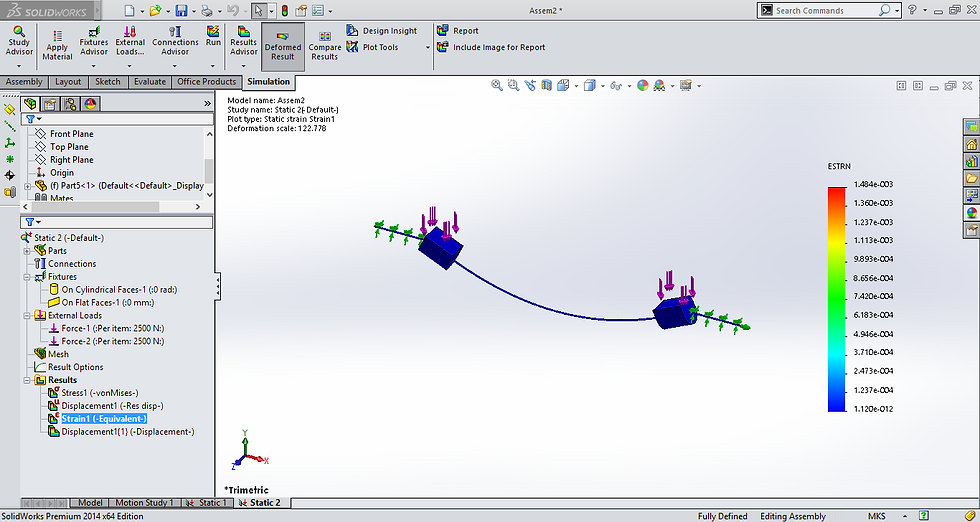
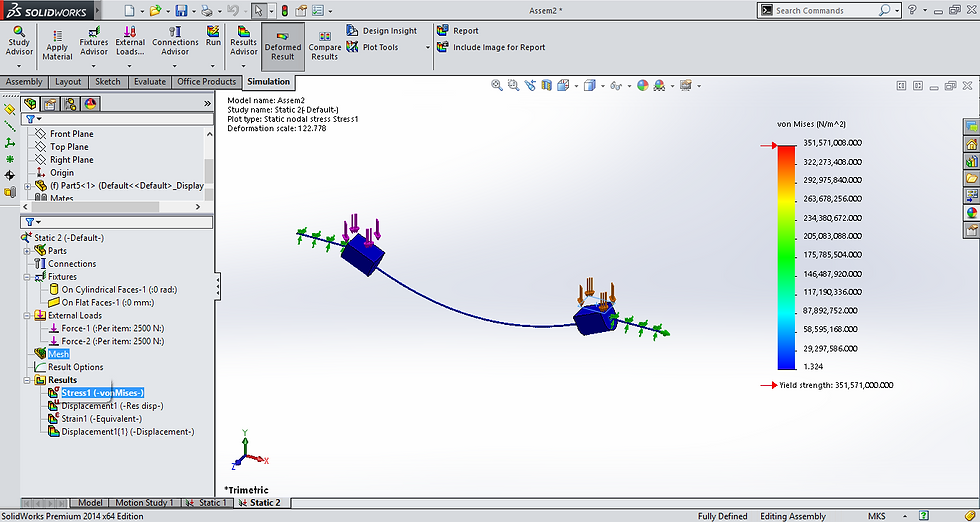
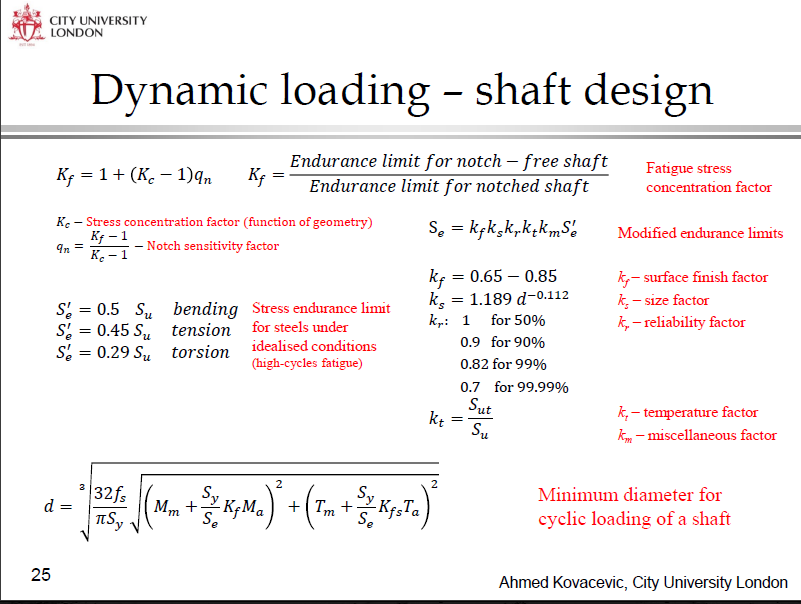


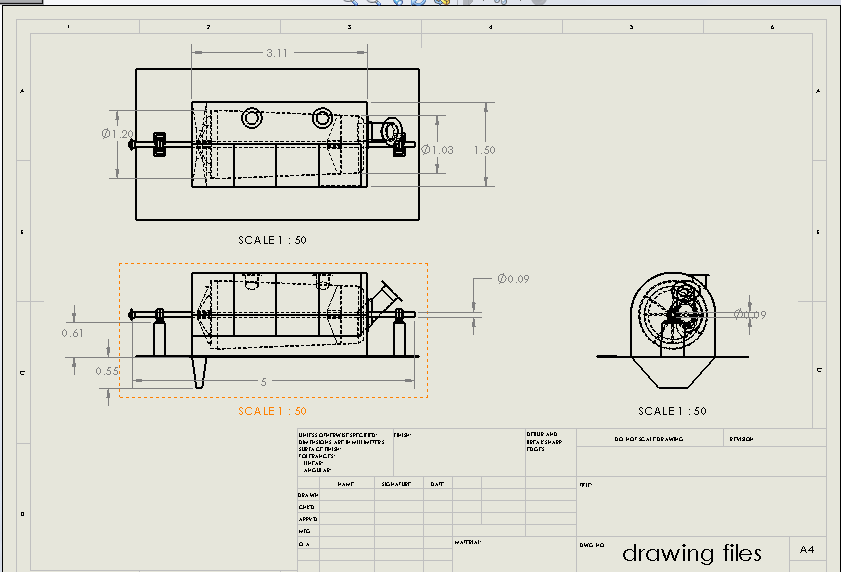

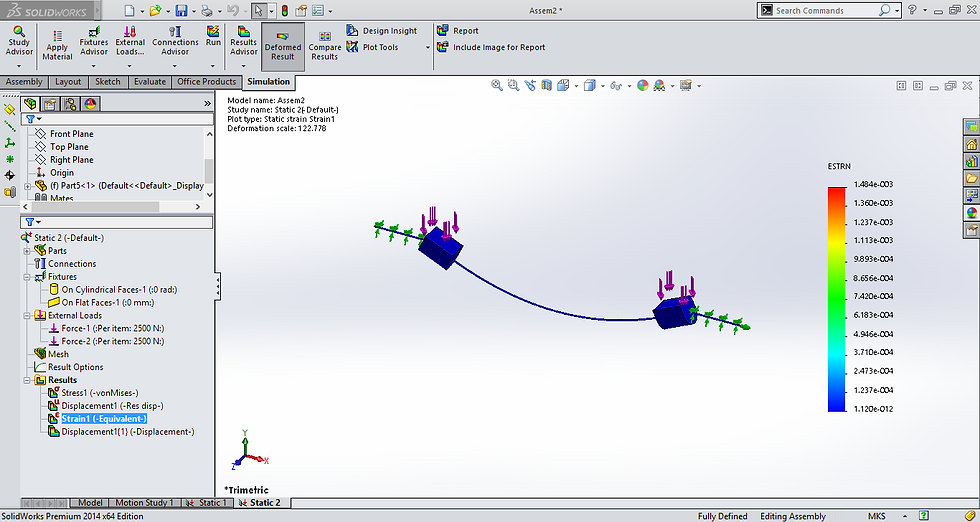
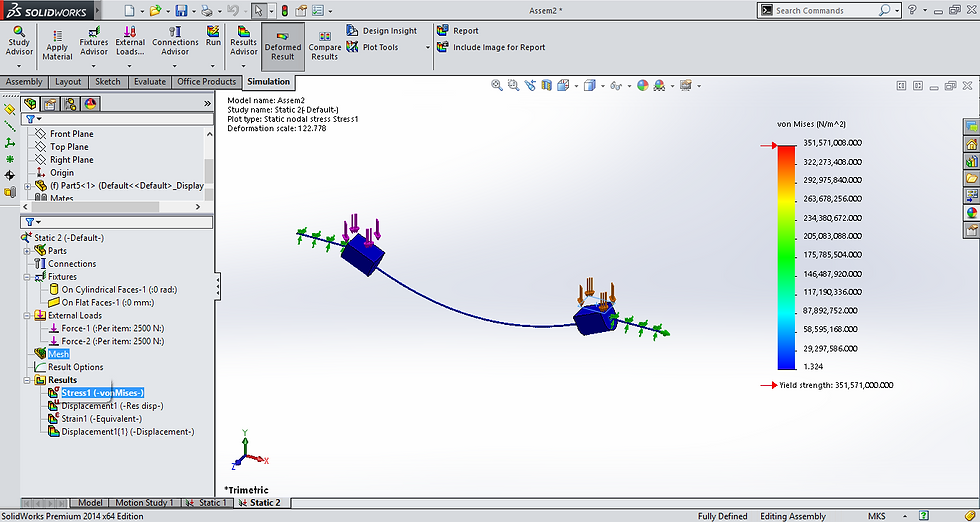
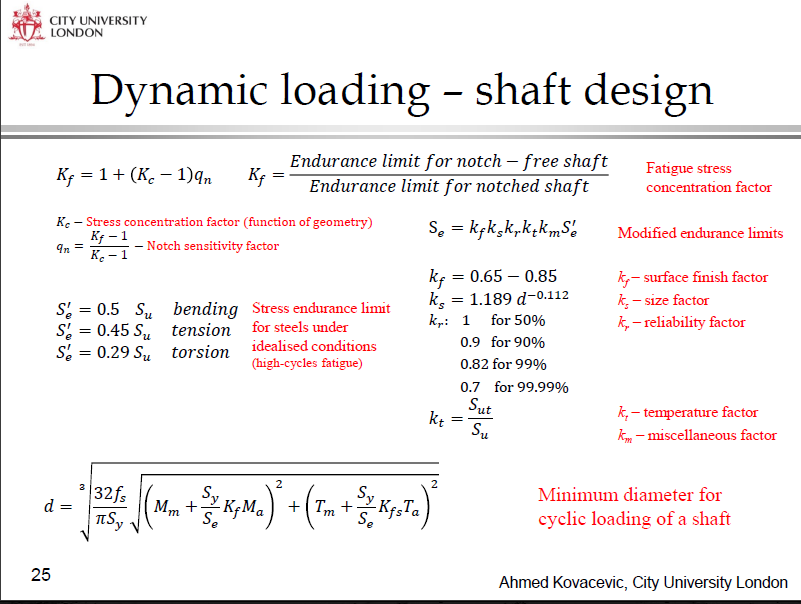
Project | 03
Project | 03 ROTARY SCREEN
​
During summer internship i worked on the rotary screen design project for raw mill 1 under direct influence of the mechanical department of the cement plant and guidance of Mr. B. Mithra (Mech. Engg). We had taken over the task of changing the current cantilever(i.e. only supported from one end) shaft system for the rotary screen to simply supported (i.e. supported from either ends) one by restructuring the arrangement and designing a whole new one for the same. This would not only improvise the performance , but also reduce maintenance cost and power consumption by reducing the load on the shaft.
As the shaft will now be simply supported therefore it’s diameter could be reduced to save material. To decide the diameter a series of hardcore mechanics calculations and manual and software analysis was undertaken based on the suitable parameters and an appropriate failure criteria.
Once the diameter was decided done we proceeded to next part of Engineering Drawing of the whole machine on Autocad Software.
Then we moved to the final part of 3D designing the whole system in Solidworks CAD software .
​
STATUS: COMPLETED




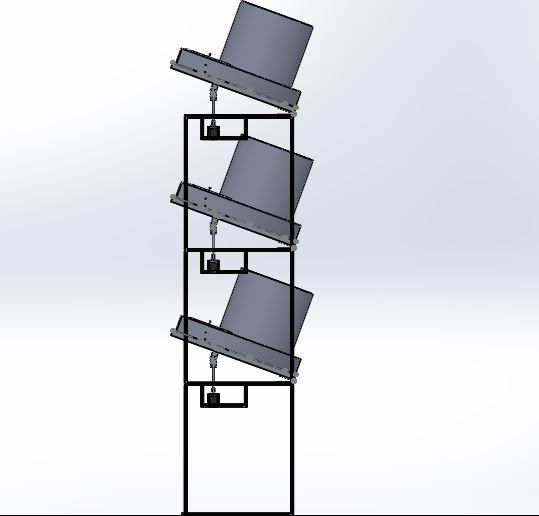




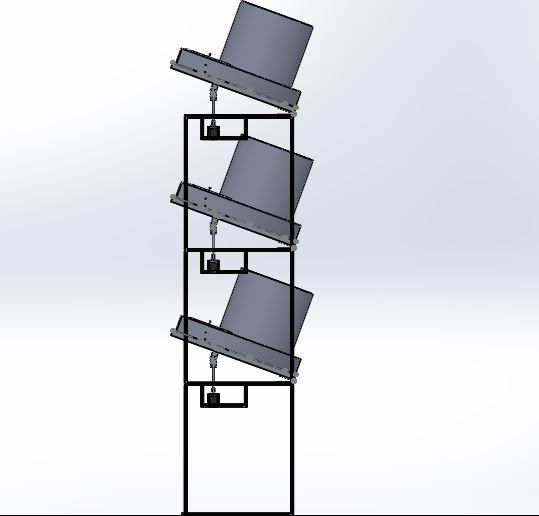
Project | 04
Project | 02 ROBOCON
​
We as a team of roughly 20 people participated in the National Level of ROBOCON 2017 Competition in which my involvement was as a mechanical designer and manufacturing and assembly lead. I also served as a mechanical assist among a team of 4 pit crew members present on site. We were to design a Disc launching bot which had to aim Styrofoam discs onto a no. of circular platforms placed at different range and heights. The bot mechanism involved locomotion system involving high torque DC motors with omni wheels, a pair of launching mechanism with high speed rotors fitted with high speed brushless DC motors and a feeding mechanism which involved a high speed striking bar which used to push a disc from the stack into the rotor which in turn launched it further. The mechanism worked satisfactorily and we were able to qualify level-1.
​
STATUS: COMPLETED